Innovation
Smarter quality control with computer vision
Discover the power of tailored AI to revolutionize your manufacturing process. In today’s fast-paced industry, quality control isn’t just a checkbox—it’s a strategic advantage that can make or break your business. At Osedea, we specialize in custom AI solutions that dive deep into your unique challenges to unlock growth, boost efficiency, and save precious time and money.
One of the most promising innovations transforming factories is computer vision for defect detection. But what is it, really? And how can it benefit your operation, no matter your size or budget? Let’s explore this game-changing technology and how it can help you leap ahead in the competitive landscape.
What is computer vision in manufacturing?
Imagine having a pair of eyes on your production line that never tire, never miss a detail, and get smarter over time. That’s computer vision in a nutshell. It’s a technology where cameras capture images of your products as they move through the line, and AI algorithms analyze these images in real time to spot defects — from tiny surface bubbles to subtle color inconsistencies or structural flaws.
But it’s not just about taking pictures. The real magic lies in how the system “sees.” Using advanced machine learning models, the computer vision solution learns what a “perfect” product looks like, and immediately flags anything outside that norm. This process is highly specific to your products and defects, making it more accurate and efficient than generic off-the-shelf options.
How does It work?
Behind the scenes, several key components come together to create an effective defect detection system:
- Optimized Lighting & Contrast: Proper lighting is critical. It creates shadows and highlights that emphasize imperfections, helping the AI distinguish defects from normal features. For example, a bubble in a coating will cast a slight shadow when lit from the side, making it stand out clearly.
- High-Speed Cameras: Depending on your production speed, cameras capture images at a rate matching the flow of products on the conveyor. This ensures no item escapes inspection, without slowing down your line.
- Tailored AI Models: Our team develops and trains machine learning models specifically for your products and defects. These models extract “features” from images — unique characteristics that help identify anomalies — and improve with ongoing data.
- Seamless Integration: The system fits right into your existing production environment, working alongside human operators. When a defect is detected, alerts or automated responses can kick in to stop the line, flag the product, or notify your team for quick action.
Why Is this a game-changer for manufacturers?
1. Save time & reduce costs
Manual inspection is time-consuming, costly, and prone to human error. Our AI-powered solution works 24/7, tirelessly scanning every product with consistent accuracy. Early detection of defects means you can fix issues before they escalate into massive waste, recalls, or customer complaints — protecting your bottom line.
2. Boost your team’s efficiency
This technology doesn’t replace your skilled operators — it empowers them. By automating repetitive visual inspections, your team can focus on higher-value tasks like problem-solving, process improvements, and strategic initiatives. It’s about optimizing your workforce, not replacing it.
3. Gain a competitive edge
In a crowded market, quality and speed set you apart. Automated defect detection lets you deliver superior products faster and with consistent standards. This responsiveness builds customer trust, opens doors to new markets, and strengthens your brand reputation.
4. Accessible for all sizes
You don’t need a multi-million-dollar budget to get started. We offer flexible proof-of-concept projects that let you test the technology with affordable hardware. We even provide cameras and equipment for initial trials — so you can experience real benefits before committing to full deployment.
The path to implementation: proof of concept (POC)
We understand that adopting new technology can feel daunting. That’s why we believe in starting small, proving value, and scaling up. Our process typically looks like this:
- Assessment & Customization: We work closely with you to understand your unique production line, defects, and goals. This lets us tailor the AI models and system setup to your exact needs.
- Pilot Testing: Using our own cameras and equipment, we set up a pilot on your line. This allows us to validate the technology’s effectiveness and gather data for refinement — all without upfront investment in hardware.
- Iteration & Optimization: Based on pilot results, we fine-tune models and processes to ensure maximum accuracy and minimal false positives.
- Scaling Up: Once proven, we help you select and install the most appropriate hardware and integrate the system fully into your production workflow.
But integrating directly into your production line isn’t the only option. We can also apply computer vision in more flexible, standalone setups. For example, we're currently working with a major manufacturer to develop an inspection station where operators can take photos of product samples at regular intervals. This “spot inspection” approach allows manufacturers to benefit from AI-powered quality control without altering their existing processes — a low-risk way to experience the impact of computer vision.
Our approach is pragmatic and collaborative. We prioritize understanding your specific challenges and constraints to deliver a solution that fits seamlessly into your operation. This way, you can test the benefits quickly, minimize risk, and build confidence before committing to a full rollout.
If you’re ready to explore how computer vision can improve your quality control and overall efficiency, we’re here to help guide you through the process — from initial concept to deployment. Contact us today to discuss your needs.
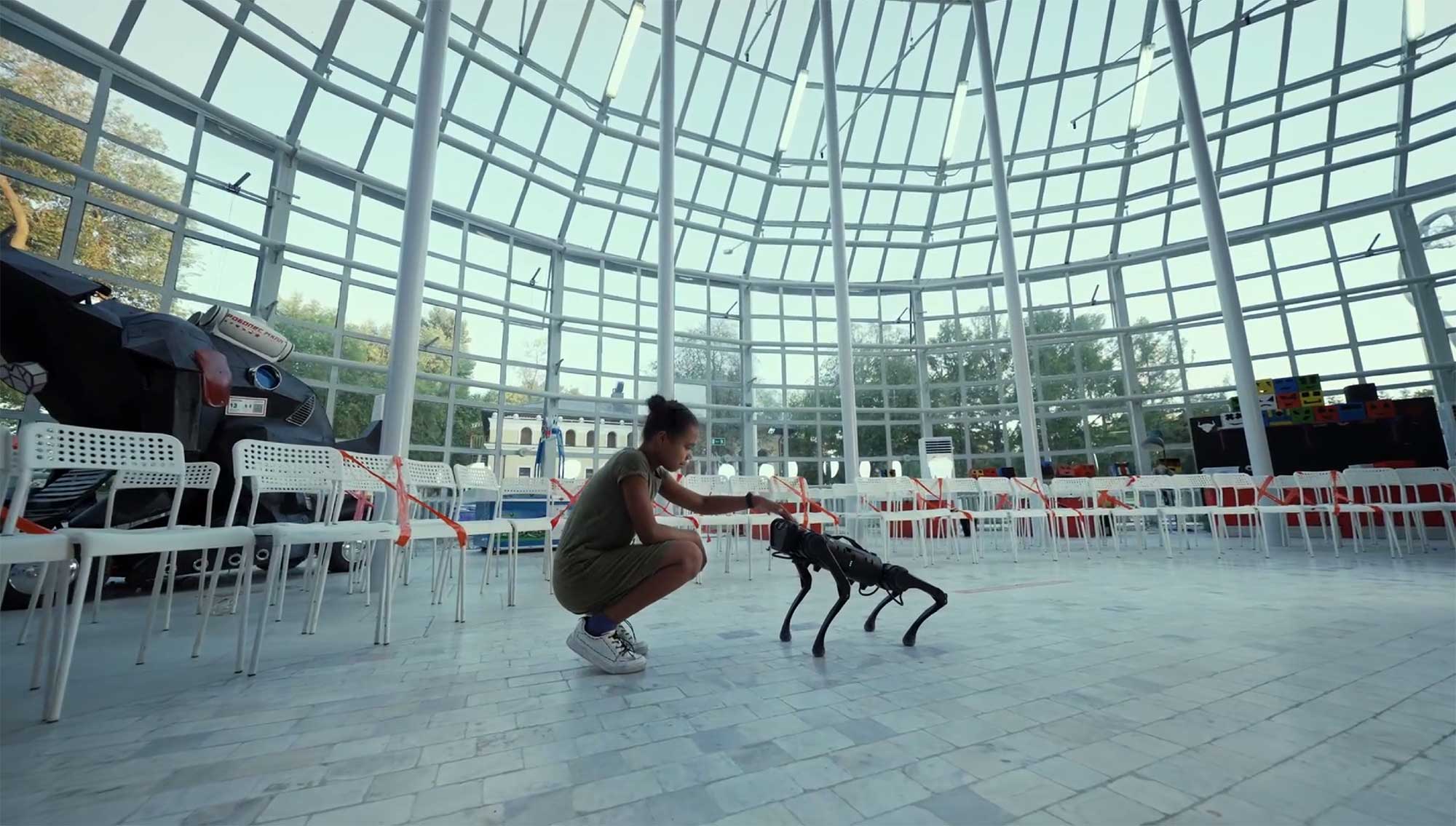
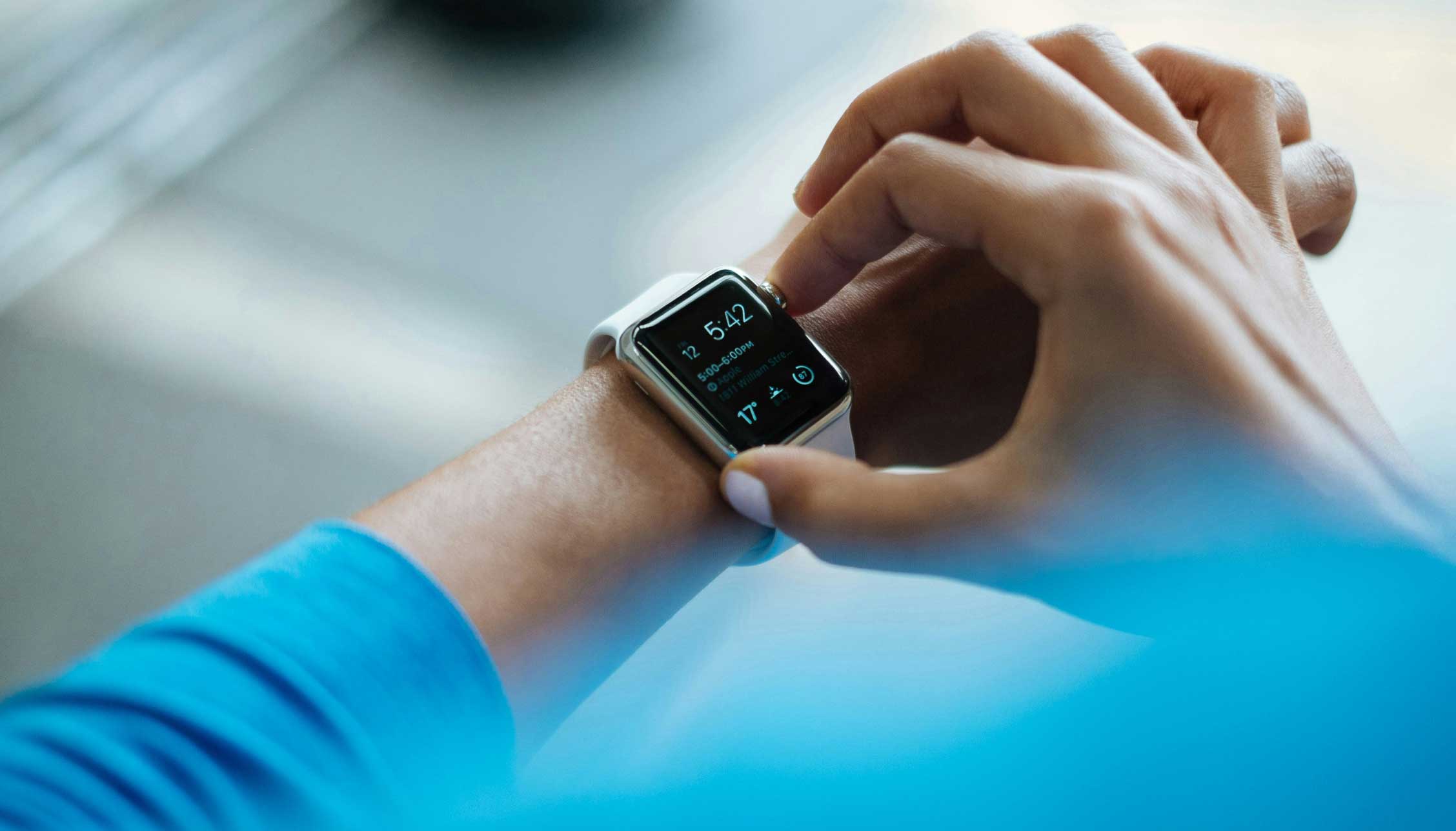
Did this article start to give you some ideas? We’d love to work with you! Get in touch and let’s discover what we can do together.